![33964148_28_10_2022_2 [Converted]-01-01.png](https://static.wixstatic.com/media/6ef6c7_5f544a22d3e44e38864a07b9d0a57a38~mv2.png/v1/fill/w_980,h_102,al_c,q_85,usm_0.66_1.00_0.01,enc_avif,quality_auto/6ef6c7_5f544a22d3e44e38864a07b9d0a57a38~mv2.png)
​Quality System
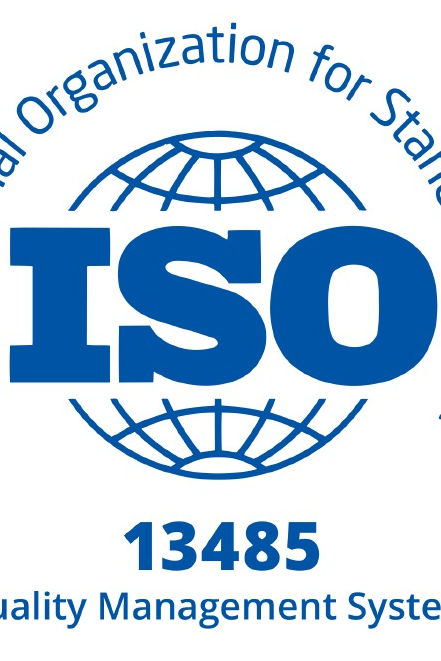
ISO 13485:2016-Certified Quality Management System
Critical Innovations is an FDA-registered medical device company (FDA Identifier: 3014021001) and is fully compliant to the FDA’s 21CFR Part 820 Quality System Regulations. Through independent, external audit the company has received ISO 13485:2016 certification (Certificate Number: PGH-2018-014) for the “Design, development, and manufacture of invasive, sterile injury-treatment devices for emergency medical treatment.”
​
All of Critical Innovations' medical device design and development activities emanate out of its ISO 13485:2016-certified Quality Management System (QMS), which the company is committed to continually improving to maintain compliance with all applicable state, federal, and international requirements. The company's QMS encompasses the full product life-cycle while defining best business practices, meeting customer requirements, maintaining stringent supplier controls, and feeding back on itself in a beneficial cycle of continuous quality improvement.
![33964148_28_10_2022_2 [Converted]-01.png](https://static.wixstatic.com/media/6ef6c7_0e979c27c71e42128d66480c3633d993~mv2.png/v1/fill/w_980,h_551,al_c,q_90,usm_0.66_1.00_0.01,enc_avif,quality_auto/6ef6c7_0e979c27c71e42128d66480c3633d993~mv2.png)
The Difference Between a Fully Functioning Quality System and Hiring a "Quality" Consultant
Fledgling medical device research and development companies in the early stages of development often attempt a limited arrangement of only having "quality" consultant or employee, without a fully defined Quality Management System (QMS). However, this approach can lead to multiple problems with achieving later regulatory clearance related to an inadequate quality system and lack of a company-wide understanding of, or commitment to, quality. There is a major difference between having a quality consultant and developing a new device under a fully implemented and active ISO 13485:2016-certified QMS.
Dangers include increased program cost, delayed speed to market, regulatory failure, and customer dissatisfaction from :
-
Inadequate design planning and history documentation of the key assumptions and decisions that resulted in design requirements and outputs
-
Deficient risk identification, analysis, elimination, and mitigation, as well as insufficient documentation of the overall risk management process
-
Being required to repeat pivotal bench-top and animal studies that were performed on "uncontrolled" product that cannot be confirmed to have met specification
-
Lack of the development of a robust quality management system required for regulatory clearance at time of submission
Working with an ISO 13485:2016 Certified Company
ISO 13485:2016 is the most recent version of international guidelines for medical device Quality Management Systems (QMS) and is recognized by the Global Harmonization Task Force as the gold standard for medical device quality management worldwide. ISO 13485 is generally harmonized with ISO 9001, but is tailored more specifically to the medical device industry and provides universal standards for the design, manufacture, export, and sale of medical devices. Achieving ISO 13485 certification demonstrates that the company has been independently audited to QMS compliance and is frequently seen as a major milestone toward achieving harmonization with U.S. and European regulatory requirements.
​
There are many benefits of working with an ISO 13485:2016 compliant company to bring a medical device to market. ISO 13485:2016 certification confirms that a company has a systematized processes for quality assurance, which ensures products are safe for their intended use and can accelerate speed to market within a stringent quality and regulatory framework. Certification communicates to potential business partners that the company is a world-class business that has met, and continues to meet, an objective standard of excellence that enhances their competitive advantage in the marketplace.

​ISO 13485:2016 certification also reduces risks associated with medical device research and development programs. A certified company by definition has an established and robust risk management approach to product development that prospectively identifies and estimates risk, while using best-practice control and mitigation techniques to eliminate hazards throughout product realization. This risk management approach facilitates a reproducible system to streamline product development and, through evidence-based decision making, reduce waste (e.g. materials, time, resources) and the likelihood of costly mistakes, while improving efficiency, speed to market, regulatory compliance, and customer satisfaction.
Quality Policy
"Critical innovations is committed to creating cutting-edge solutions to health threats that span pre-hospital, hospital, and military environments. We are committed to supplying products and services that exceed the customer's requirements and expectations on a consistent basis.
​
We conform to all established regulations and provide an environment that encourages innovation and prevention of defects.
We understand that quality is everyone’s responsibility; we will do all that we can to meet the customer and regulatory requirements every time.
We foster a culture whereby all employees are encouraged to strive for excellence and continue to improve and maintain the effectiveness of the quality system."
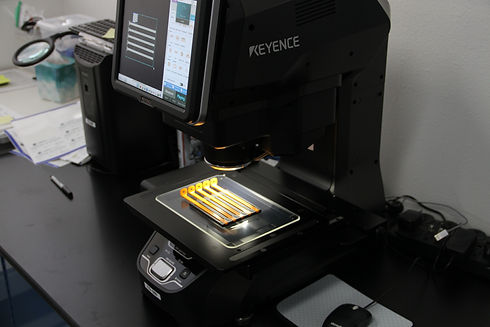
CD010 Rev.P 2025-01-31